Forced by new regulations lubricants manufacturers worldwide are replacing the mineral base oils in metalworking fluids by natural sourced derivatives.
Behind the hype of bio-based metalworking fluids
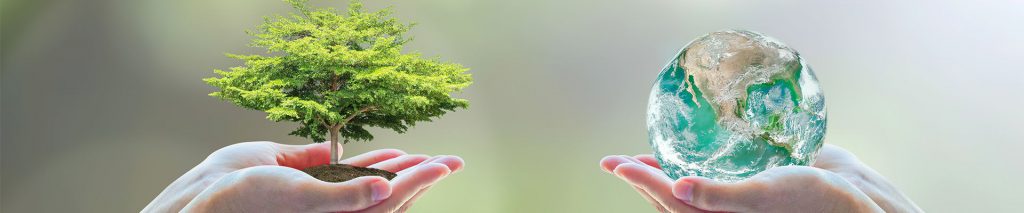
Forced by new regulations lubricants manufacturers worldwide are replacing the mineral base oils in metalworking fluids by natural sourced derivatives.
Stainless steel is often considered difficult to machine. While using the right machinery and tools for the job is most important, choosing the most effective metalworking fluid can help overcome common machining problems.
Getting the most from your metalworking fluid is all about choosing the correct equipment. Using the right equipment makes it possible for you to enhance the life of your fluid, improve its longevity and prevent problems in the future. So, what equipment should you use?
Our first priority is the health and safety of the machine operator and other people within the vicinity of the machine. Our Q8 Brunel range is designed to provide the optimum balance of protection against microbiological contamination without the need for using unnecessarily harmful chemicals providing a safe working environment.
Q8 Brunel XF 527 is an advanced non-cobalt leaching synthetic grinding fluid developed to give the highest quality finish in all operations. It contains no mineral oil and is free from boron, formaldehyde, nitrite and secondary amine. When diluted with water it forms a true solution rather than an emulsion which gives excellent wheel and work piece visibility. Q8 Brunel XF 527 uses the latest in fully synthetic anti-corrosion additive technologies and has outstanding corrosion protection, suitable for all ferrous metals giving rust and stain free machining.
Based in Hertfordshire, UK, Pope & Meads is a long-established precision engineering company providing solutions for scientific, defence and aerospace sectors. Services include ultra-high precision machining; general machining; electro-mechanical assembly; cleanroom assembly; parts and material sourcing; specialist finishes/treatments; testing and verification; inspection and reporting; and product cleaning.
The Q8 Bach XNRG bio-lubricants exceed the EN 16807 requirements, combining excellent cutting performances with an eco-friendly character.