This series of articles focuses on five aspects of emulsions for copper wiredrawing that manufacturers must focus on to maximize their productivity and reduce production costs.
Introduction
Today’s global working environment poses economic challenges for manufacturers, making increased factory productivity a key for successful growth. That makes it important for companies to be able to measure productivity and understand what aspects are important to increase it. This paper highlights processes used to measure and extend the productivity of a copper wiredrawing emulsion to reduce factory production costs and increase the performance of a wiredrawing machine.
Many principles on changing productivity are widely known. Lean Thinking, Six Sigma and Kaizen and other methods are all used to highlight problematic issues, evaluate procedures, streamline production and make changes for improving productivity.
Evaluation
A simple way to increase the productivity of a copper wiredrawing emulsion is to evaluate the process in several steps of the life of the product to provide a broad overall perspective of managing the emulsion, as well as practical advice to enable the best performance from the systems. The evaluation steps include:
- drawing lubricant technology,
- housekeeping of the emulsion system,
- performance of the drawing emulsion,
- technical support by the supplier,
- evaluation of disposal techniques and costs.
Drawing lubricant technology
Copper wiredrawing lubricants are highly specified soluble oils designed for mixing into water at concentrations from 2 to 15% dependent on specific application, and it is important to understand the technology in the product.
A soluble oil concentrate for wiredrawing will typically contain the following chemical types of additives:
high quality mineral oil | lubricity additives |
oxidation stable pure base oils | extreme pressure performance additives |
emulsifiers | bactericides |
surfactant detergency additives | biocides and fungicides |
surfactant coupling agents | antifoams |
corrosion inhibitors | water |
Users need to understand the physical and chemical properties of soluble wiredrawing emulsions so they can effectively manage their use and appreciate why precautions and procedures should be followed.
Wiredrawing lubrication
Wiredrawing lubricants provide both boundary and hydrodynamic lubrication. Boundary lubrication is a thin film, primarily at slow speeds, between the wire/die interface and the wire/capstan interface. Hydrodynamic lubrication is a thin film at the wire/die interface at high speeds. Wiredrawing lubricants can be conventional, semi-synthetic or fully synthetic, each with different lubrication properties. Semi-synthetic products are oil in water emulsions and the suspended oil droplets range in size from 0.8 to 1.0 microns in diameter. This is the most common wiredrawing lubricant for copper. The droplets provide lubrication at both the die and capstan surface. They also clean surfaces, thus simultaneously placing lubrication films and removing them.
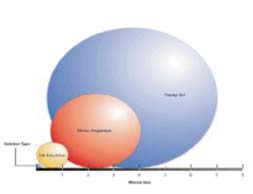
The effects and comparison of oil droplet size.
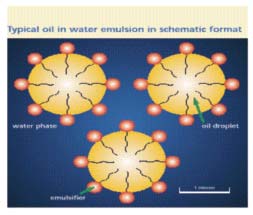
The oil droplet with emulsifiers attached.
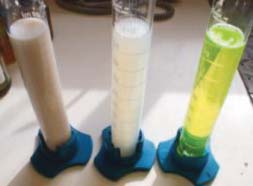
The effect of oil drop particle size in an emulsion. The oil droplet size is directly related to the emulsion characteristic appearance, left to right, semi-translucent to translucent to clear.